Oil and Gas sector
We are the experts in the business of temperature control in Oil and Gas and have worked with all the refineries in India. Some of our major refinery customers are HPCL, IOCL, BPCL, Reliance Industries Ltd (Jamnagar/Dahej), BORL, Nayara, HMEL.
We also work with Shutdown contractors like Sulzer, CR Asia, Radiant Hitech. Even EPC mojors like L&T is our client.
Hydrocarbon sector is considered as the most hazardous industry where safety is of prime importance. We have executed all our jobs without a single incidence of safety.
HVAC equipment is required in the following equipment in refineries:
- Columns
- Reactors
- Vessels
- Tanks
- Underground bullets
- Above ground bullets
- Silos
- Revamp jobs including heavy hot work
- Furnace
Application of Temperature Control Equipment of Mark
Columns Vessels Reactors
During shutdown/turnaround, revamp jobs are performed in column, reactors, vessels to increase the capacity of the equipment. This requires heavy hot work to change the configurations of column/reactor internals, tray support rings. Temperature rises inside due to continuous welding and also creates smoke inside. Our equipment can maintain comfortable working condition inside the confined space by reducing the temperature between 23-26°C and humidity level of 55-60%. This helps to increase the productivity and also provides the right environment required for welding to avoid porosity.
Ventilation inside the confined space is provided with blowers which removes the smoke out of the system.
Reactor, Furnace and Sulphur pit cooling
Catalyst is present inside reactor which emits high heat even when the reactor is shut down. The temperature inside the reactor is approx. 900°C to 1100 °C. Reactor is allowed to cool down from 1100°C to 250 °C using natural draught which consumes 3-4 days of shutdown. The equipment is then handed over to us at 250°C. We further reduce the temperature of reactor from 250°C to 40°C in flat 8-12 hours saving crucial shutdown time.
Faster cooling of the reactor is required to perform maintenance operations or for catalyst loading/unloading jobs. In shutdown, client cannot depend only on natural draught cooling of the reactor as it can be very time consuming thereby disturbing shutdown schedules. In such situation, artificial cooling of the reactor is achieved by using our equipment.
Workers are then allowed to enter inside the reactor and gradual cooling of reactor is achieved up to 23-26°C. It helps to achieve the tight shutdown schedules which otherwise is practically impossible without the HVAC/Dehumidification systems.
Sulphur pits also has very high temperature and presence of poisonous gases like H2S. Pits are cleaned by workers with manual entry and use of SCABA. Mark dehumidification equipment is used to reduce the temperature inside the sulfur pits.
Reduction in furnace temperature and heating of refractory after application for dry out can also be achieved by our equipment.
Oil and Gas Sector
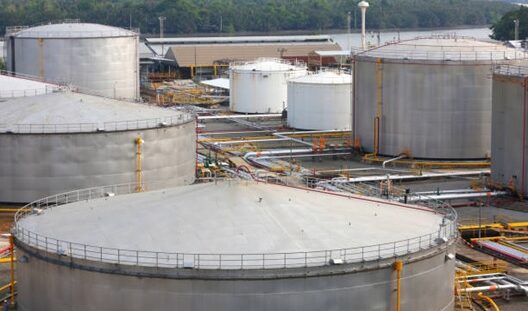
Maintain right humidity levels during painting and coating jobs in Tanks is very essential for uniform paint/coating application. Presence of moisture/dew during painting will create bubbles/pores in the applied paint which will not meet quality specifications. Our equipment can help you to maintain the humidity levels between 40 to 60 and controlled temperature. Hence, you can now carry on with our blasting, painting, coating jobs irrespective of the weather condition.
Cooling inside the tank is also required during tanks modification / revamp or construction. Tank Pantoons, bottom plate is to be welded during repair.
Proper ventilation and controlled temperature in bullets above and below grounds.
Silo Maintenance
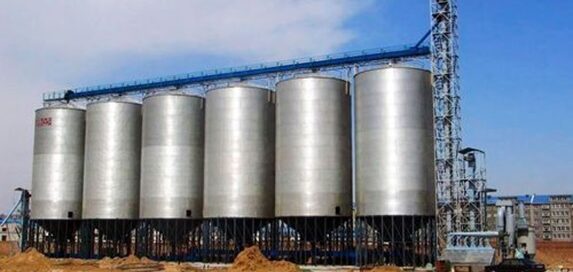
Silo’s need frequent maintenance to protect the mother plate from erorion and protect rubber lining. To protect the mother plate from erosion, Hardox plates are welded to mother plate. This requires super precision welding inside the confined space. Silo has only one entry point from the top.
Maintaining proper temperature and environment inside the Silo during Hardox plate installation job is very crucial for workers to perform. Mark can come to your rescue & achieve the right temperature levels along with induced draft ventilation system through blowers.
Preservation of turbine and critical equipment during an idle period
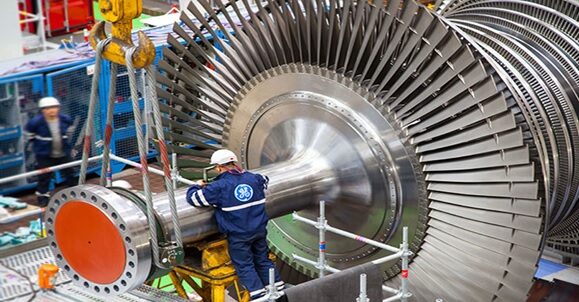
During shutdown/turnaround of oil refineries, the critical equipment has to be kept idle. This equipment has to be prevented from moisture to avoid rusting. Corrosion can be controlled through dehumidification. During a shutdown, relative humidity should be maintained at 15%-30% RH at 24ºC (75ºF) and during operation.
Mark offers the simplest and the most effective solution for humidity control for preservation. MARK provides desiccant based Dehumidifiers, which maintains the right humidity conditions for the preservation of critical equipment in the oil and gas industry.