Sugar Industry
Importance of sugar drying and cooling Cooling, and in particular conditioning, is the final step of white and refined sugar production. It transfers the sugar into a stable condition for storage, packaging and transportation. The maximum residual water content depends on sugar quality and should be in the range of 0.03% to 0.04%, while the maximum temperature, which depends on the customer’s specifications, climatic conditions, and available silo technology, has to be between 25 °C and 40 °C. The finished product must be free from sugar lumps.
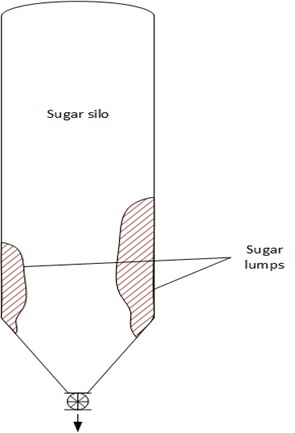
Depending on ambient conditions, freshly produced sugar can lose its water-binding properties again within a relatively short time (within the first one to two days), i.e. it releases part of the bound water. In silos or in the packed sugar, this released water can cause lumps and caking.
Crystal sugar is very often stored in large silos >30 m3 that are supplied by trucks or railcars. Many sugar lumping, caking, more generally flow problems out of the silo are however experiences by factories.
Sugar flow problems in silo
What are the problems observed in sugar silos?
The most widespread issue reported by factories around the world operating sugar silos is the caking (lumping) of the sugar stored which leads to flow problem, quality problems, reduction in storage capacity and factory output, and in some cases, safety problems.
Sugar, in certain conditions, has the ability to form lumps, which can harden and get bigger with time. In extreme cases, blocks of several dozens of cm can be found in silos, typically along the silos walls. This hard sugar cannot easily be taken out of the silo.
The presence of these large lumps is reducing the useful volume of the silo, can lead to blockage if lumps are falling down and obstruct the outlet of the silo. In certain cases, if a very large block suddenly falls, it can even damage the structure of the silo and impact the cone.
Root causes of sugar lumping?
Why do sugar lump in silo?
The main root cause of sugar caking in silos is humidity transfer within the bulk, happening especially near the walls of the silos, and is compounded by other aggravating factors such as an incorrect flow pattern in the silo.
Humidity
Sugar loaded to silo has a certain humidity. The level of humidity is usually not a problem for the sugar itself, but once loaded in a silo, if the silos walls are cooled down enough for example at night during the cold season, temperature near the sugar silo walls can fall below the dew point and condensation can happen in the area close to the wall. As sugar is soluble in water, tiny parts of it dissolve, when it dries again, for example when the sun lights and heat up the silo again, the water evaporates and the dissolved sugar cristallize creating solid bonds in between sugar particles, which leads to lumping, often adhering to the silo walls.
Repeating this cycle can lead to harder and bigger sugar lumps.
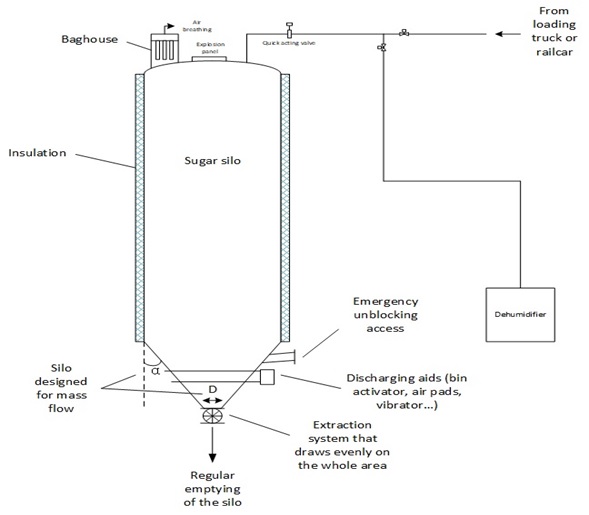
How to solve sugar flow problems in silos?
Solutions to prevent sugar lumping in silos
The proposals presented below should be considered for all new silos aimed at storing sugar in large quantities, factory operators should discuss them with their suppliers in order to select the appropriate ones. However it can be possible to retrofit existing silos, in case the considered silo is not equipped with those features and is experiencing sugar lumping, caking and flow problems.
Air conditioning
The conditioning of the air inside the silo can help in alleviating some lumping issues with sugar. Dry air blanketing will indeed avoid that humid air from the external environment is penetrating the silo and transfer water to the sugar that can lead to caking (see paragraph 2). It can also help in removing excess moisture in the sugar stored but, if the air conditioning is only introduced at the top of the silo, this will have a limited effect.
To air condition the silo in the range 20-25c and 50-60% RH, a standalone dehumidifying system can be used and connected via pipe to the top of the silo.